LLOYD Industrial Parts - Your expert for Metal Injection Molding (metal powder injection molding)
At LLOYD Industrial Parts you are on the edge of progress.
We fuse German engineering standards with international resources to provide you with cost-effective Metal Injection Molding (MIM) solutions.
What we do.
Your expert for Metal Injection Molding (metal powder injection molding)
The MIM process is an innovative approach to producing complex geometric metal components in high volumes.
It combines the advantages of plastic injection molding with those of powder metallurgy. The result is complex components with incredible precision and outstanding mechanical properties, with cost-efficient production.
Are you ready to take the next step in component manufacturing?
Contact us today for a free quote or an immediate consultation on MIM.
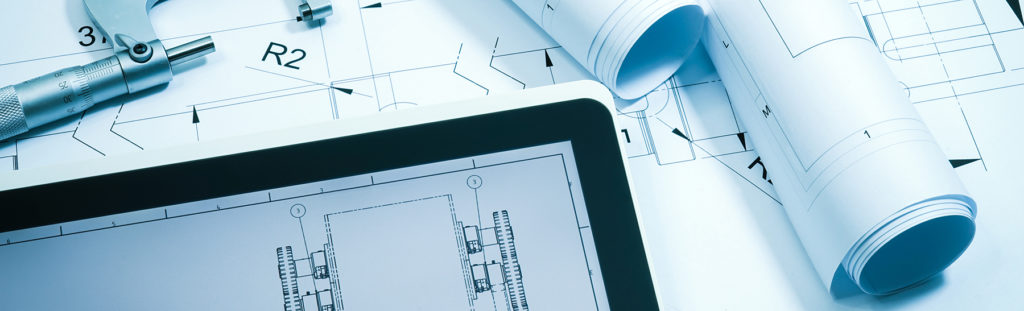
Our quality promise.
LLOYD Industrial Parts - MIM - Metal Injection Molding.
At LLOYD Industrial Parts, we bring innovation and quality together under one roof.
Our strong position in the market is the result of years of experience and extensive expertise in metal processing.
In keeping with Hanseatic tradition, quality and customer satisfaction are our top priorities. That is why we rely on first-class casting processes, experienced production partners and stringently controlled production processes.
Our expertise and dedication to quality, are reflected in every component that leaves our warehouse.
- Low unit costs and tooling costs
- High dimensional accuracy
- Cost efficiency
- High quality standards
- Production of medium and large series
At LLOYD Industrial Parts, we are proud to utilize this future-oriented technology and lead our customers to the forefront of manufacturing innovation.
Discover the advantages of innovation and quality from a single casting – with LLOYD Industrial Parts.
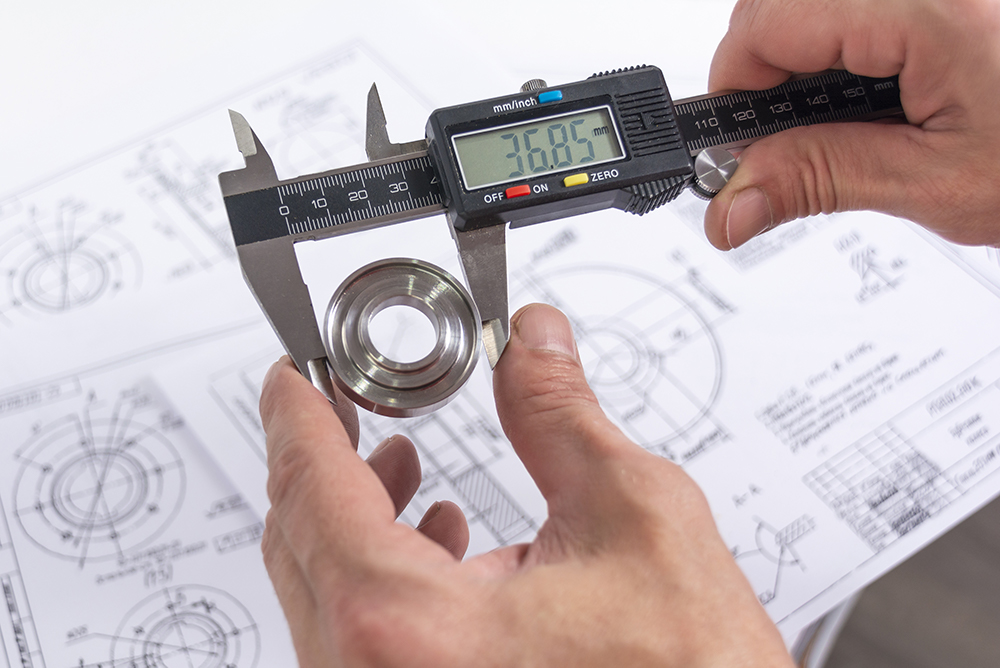
MIM convinces with precision. With a dimensional accuracy of +/- 0.5%, even structures important to detail and precise contours can be reliably manufactured.
Parts produced in the MIM process impress with excellent surface quality, which often requires little post-processing.
MIM parts achieve a high relative density of 95%+, resulting in excellent mechanical properties.
With the MIM process, the complexity of your components has no limits. Whether fancy geometric shapes or complex details, our innovative production processes allow extensive design freedom.
In this way, design ideas become reality within a very short time.
The MIM process offers almost limitless design possibilities. Even complex, structures can be realized.
Our cost-optimized production model allows low unit and tooling costs – without compromising on quality.
Thanks to the high production speed and efficiency of the MIM process, we are able to keep our costs low. Advantages that we can pass on directly to our customers.
MIM is not only economical for large series, but also for medium quantities.
To ensure a stress-free and smooth process from order to delivery, we offer a comprehensive service, including “free house” deliveries.
In doing so, we take over the complete processing and ensure that your components reach you safely, promptly and in top quality.
Your advantages.
Metal Injection Molding: A step into the future
Metal Injection Molding (MIM for short, or metal powder injection molding) is an innovative form of metal processing that combines the advantages of traditional casting methods with those of modern plastic injection processes.
MIM technology marks a decisive step into the future of metalworking, thanks to its ability to realize fine details and complex geometric shapes with high productivity and precision.
The MIM process begins with the production of a mixture of metal powder and a binder polymer, also called “feedstock.” This is then injected into a mold, similar to plastic injection molding. After injection molding, the binder is removed from the so-called “green part” in a debinding process that can be either thermal or chemical.
The remaining metal part is then sintered in a high-temperature process, giving it its full density and desired physical properties.
The MIM process is particularly well suited for high-volume production of parts where complex geometry, tight tolerances or special physical properties are required.
At the same time, it competes strongly with traditional casting and machining processes because it typically requires less post-processing of the part and therefore results in lower overall costs.
At LLOYD Industrial Parts, we are proud to leverage this cutting-edge technology and help our customers stay at the forefront of manufacturing innovation.
Are you interested?
Contact us today for a free quote or immediate advice on MIM.
Our process.
Step by step:
From mixing and casting to the final product.
1. Contact us
Your innovation project starts with contacting our team at LLOYD Industrial Parts. Here we discuss your specific requirements, project parameters and the desired properties of your MIM components.
2. Offer
Based on our initial discussions and taking into account your requirements and needs, we create a tailored offer for you. This will transparently and clearly list all cost factors and delivery dates.
3. Tool construction
The third step is tool construction. Our experts at LLOYD Industrial Parts design and build the tool required to manufacture your MIM part. Here we use state-of-the-art CNC technology and follow the strictest quality control standards. The tool design is based on the previously defined product parameters and the specific requirements of your project. This process ensures the precision and quality of your MIM component and is an essential step on the path to production.
4. Mixing and casting
Your project moves into direct production preparation by mixing the metal powder with a binder to form a "feedstock". This process is carefully monitored to ensure a uniform and high-quality mixture. The prepared feedstock is then injected into a mold, a process similar to plastic injection molding. This results in a "green part", i.e. still unsintered product that already has the final shape of your component.
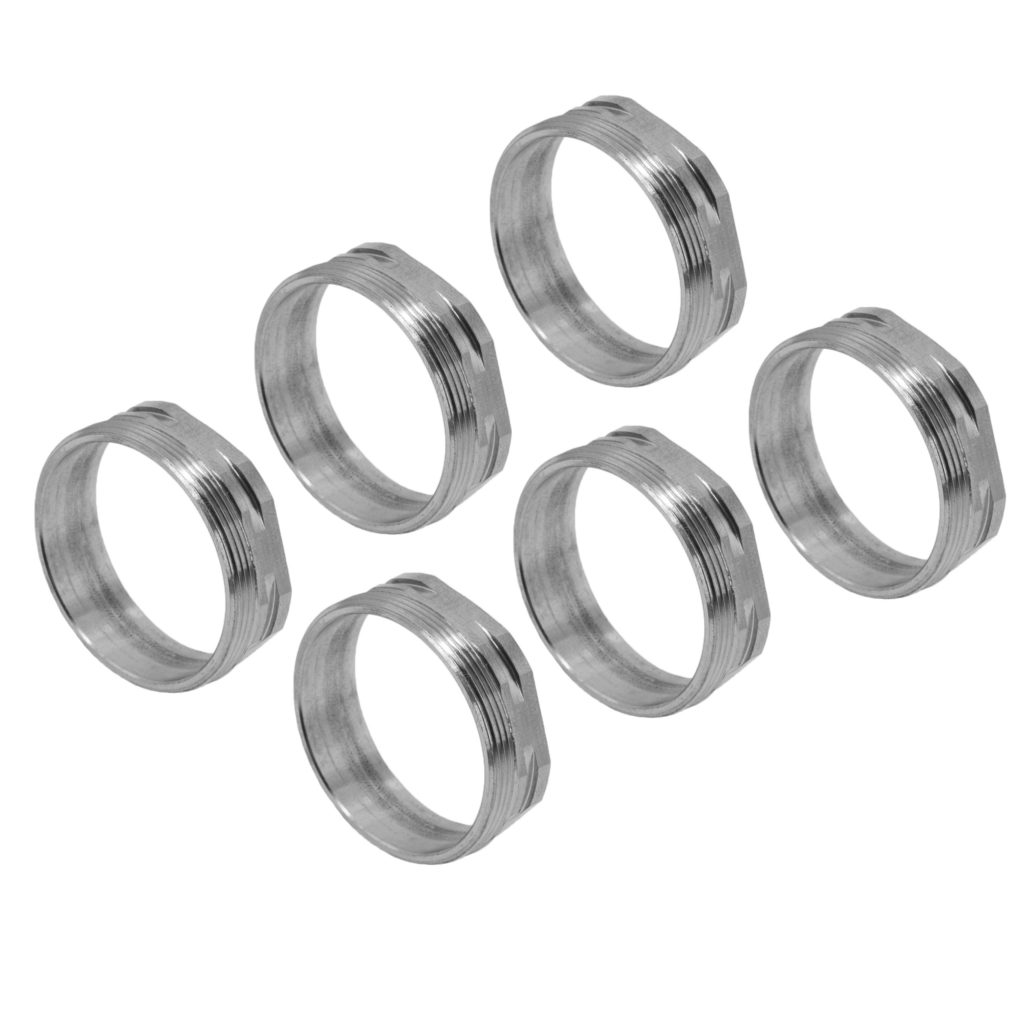
5. Sintering
Next, the component is sintered. It is exposed to a high temperature that is below the melting temperature of the metal particles in order to fuse them together and achieve the full density and desired physical properties.
6. Debonding
In this step, the binder is removed from the "green part". This is done by a chemical or thermal process and is essential for the quality of the final product.
7. Final inspection
After sintering, a strict final inspection takes place. Here, the precision, tolerances and quality of the final component are thoroughly checked to ensure that it meets your requirements exactly.
8. Optional: post-treatment
LLOYD Industrial Parts then offers a comprehensive range of post-treatments to ensure that each part meets our customers' individual requirements.
9. "Free home delivery"
After successfully completing all quality assurance measures, the finished MIM component is prepared for shipment. Thanks to our comprehensive service, delivery is made directly to your doorstep. We take care of all logistics details so you can focus on your core business.
FAQ
Frequently Asked Questions
In which industries is MIM used?
MIM is used in a variety of industries, including automotive, aerospace, electronics, medical technology, and many more. It is particularly suitable for the production of components that require high precision, detailed and complicated shapes.
What are the advantages of MIM over other production processes?
Some of the main advantages of MIM include the ability to produce very complex shapes with high precision, the capability to use a variety of metals and alloys, lower per-unit costs at higher production volumes, and reduced post-processing of parts.
Can MIM be used for all metals?
MIM can be used with a wide range of metals and metal alloys, including steels, nickel alloys, cobalt alloys, titanium, copper and more.
Are MIM parts as strong as conventionally manufactured metal parts?
Yes, MIM parts can have comparable or even superior mechanical properties compared to conventionally manufactured metal parts. The density of MIM parts typically reaches 95-98% of the theoretical density of the metal, resulting in high strength and durability values.
What post-treatment processes are possible?
With these post-processing steps, LLOYD Industrial Parts provides everything from one source: from production to final processing and adjustment of the MIM parts.
We guarantee that every product that leaves our house is custom-tailored to our customers and meets the highest quality standards.
Surface finishing
Our experts are able to perform a variety of surface treatments, including sandblasting, vibratory grinding, hardening, electroplating and painting. These processes can be used to enhance the appearance of the part, highlight specific physical or chemical properties, or increase the durability and resistance of the product.
Ideal for small parts
Series production of components from 0.1g to 200g possible.
Cutting-edge machining
LLOYD Industrial Parts also offers a range of machining services, including turning and milling, grinding and reaming, honing and drilling. These allow us to make even the finest contour or shape adjustments to the parts to perfectly match the customer’s requirements.
Thread cutting
We can also offer thread cutting, which allows for high precision and quality threads. This process can be applied to MIM parts as well as to other components.
Is it "Metal Injection Molding" or "Metal Injection Moulding"?
Although both terms refer to the same process, they simply reflect different spellings in different parts of the English-speaking world. In the USA and in American English in general, it is common to write “Metal Injection Molding” with “molding”. In British English, however, the spelling “Metal Injection Moulding” with “moulding” is more common. Both terms are correct and interchangeable, depending on which spelling conventions one follows. At LLOYD Industrial Parts, we use both terms according to context and target group.
How long does the MIM process take?
The exact duration of the MIM process depends on several factors, including the complexity of the part design, the quantity of parts, and specific project requirements. For a more accurate time estimate, please contact our team at LLOYD Industrial Parts.
At what volumes is MIM economical?
MIM is particularly economical at medium to high volumes. The exact quantity depends on many factors, such as the complexity of the part and the specific project requirements. We will be happy to advise you individually on your project.
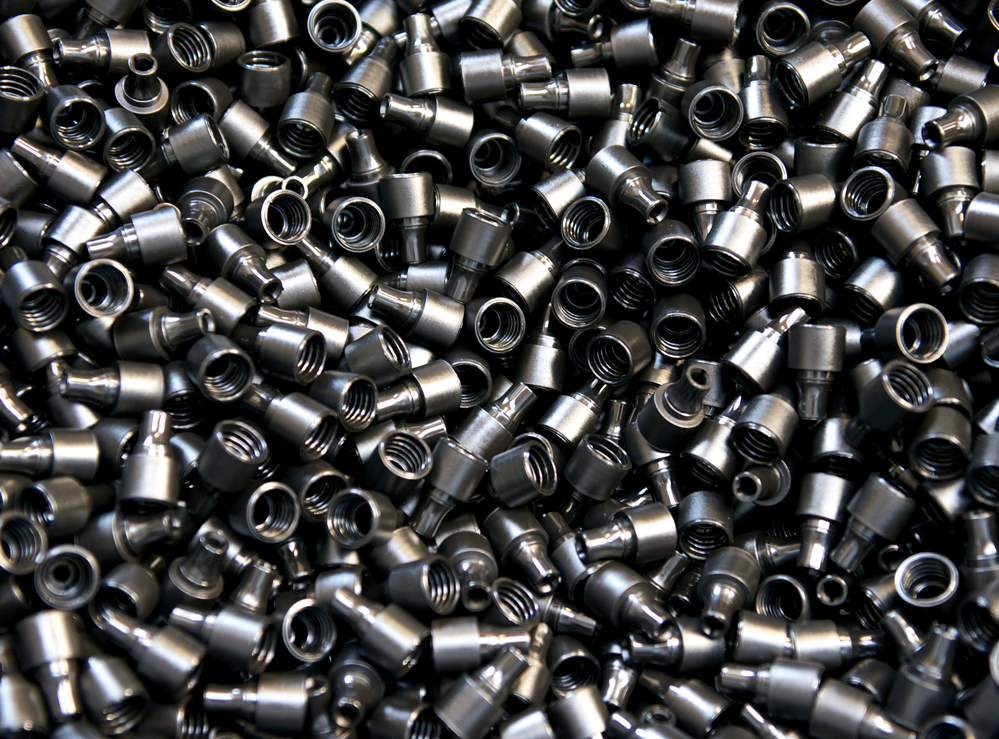
CONTACT US.
Request an individual quote or a free consultation now.
We invite you to take the first step and contact us – by phone, e-mail or via our online contact form on our website.
According to the North German motto: Simply ma’ report.
E-Mail: info@lloyd-parts.de
Phone: +49 421 835 265 20
Service offer
Further services
In addition to our core competency in metal injection molding, we provide a wide array of extended services that can optimize and simplify your production processes.
Investment casting
Investment casting is synonymous with precision and attention to detail, making it ideal for complex components with specific requirements. At LLOYD Parts, we provide a comprehensive investment casting service. Our expertise enables the manufacture of components with tight tolerances and exceptional surface quality.
CNC manufacturing
Thanks to state-of-the-art CNC-controlled machines, we guarantee precise and efficient machining of your components. Various CNC milling and turning processes enable us to quickly and efficiently realize complex shapes and contours according to your individual specifications.
Component assembly
Our range of services also includes the assembly of components. We take on the assembly and adjustment of individual parts into functional units, allowing you to focus on your core competencies. With state-of-the-art technologies and precisely according to your requirements, we assemble efficiently and with high quality.