LLOYD Industrial Parts - the traditional Hanseatic company for industrial precision casting.
Welcome to LLOYD Industrial Parts, your expert for investment casting based in the traditional Hanseatic city of Bremen.
In the dynamic world of mechanical engineering, quality, precision and efficiency are of vital importance. With years of expertise, our team of experts, deeply rooted in old Hanseatic tradition, meets the industrial demands of the science of investment casting.
What we do.
Your expert for investment casting.
In the dynamic world of mechanical engineering, quality, precision and efficiency are of vital importance. With years of expertise, our team of experts, deeply rooted in old Hanseatic tradition, meets the industrial demands of the science of investment casting.
Located in the heart of Northern Germany, we offer you the highest quality for individually manufactured investment castings (small and large series) and a comprehensive customer service that does not forget personal contact in addition to high technical expertise.
Convince yourself of our expertise. Contact us for an individual offer or a free consultation.
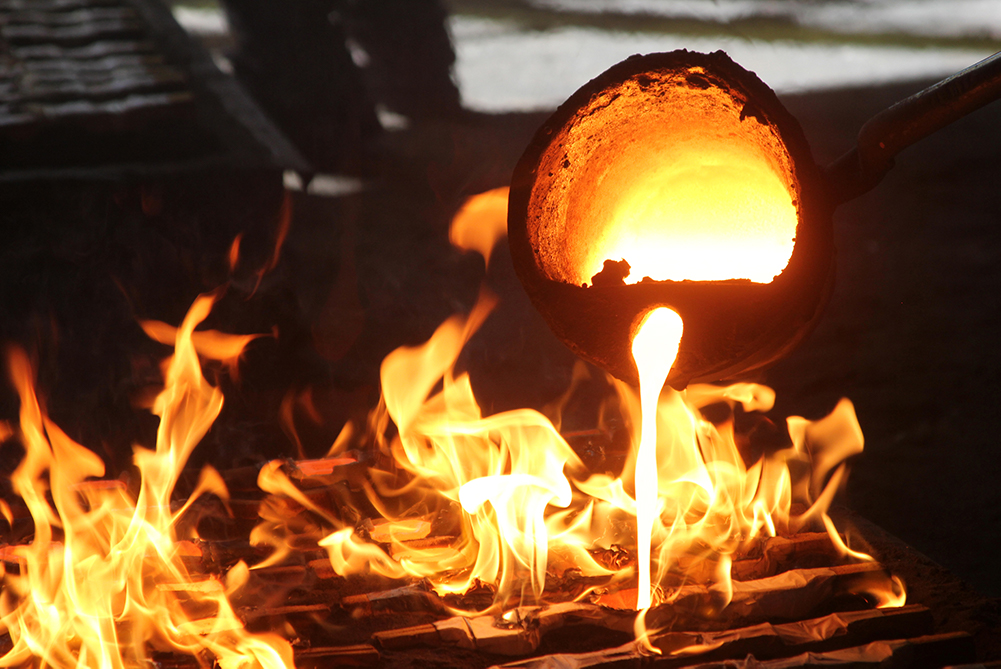
Our quality promise.
LLOYD Industrial Parts: Innovation and quality from a single source.
Thanks to many years of expertise in investment casting, we are able to produce complex and precise parts for you.
Compliance with the highest quality standards is a matter of course for us. Our integrated quality management system guarantees that every product that leaves our warehouse meets our strict quality controls.
The use of state-of-the-art technology and efficient production processes allows us to keep costs for components and tooling costs low without compromising on quality.
- Years of expertise in investment casting
- Competitive prices
- High dimensional accuracy
- Cost efficiency
- High quality standards
- Production of small and large series
At LLOYD Industrial Parts, we set a high value on individual solutions and personal advice. Quality, performance, and customer proximity are our top priorities.
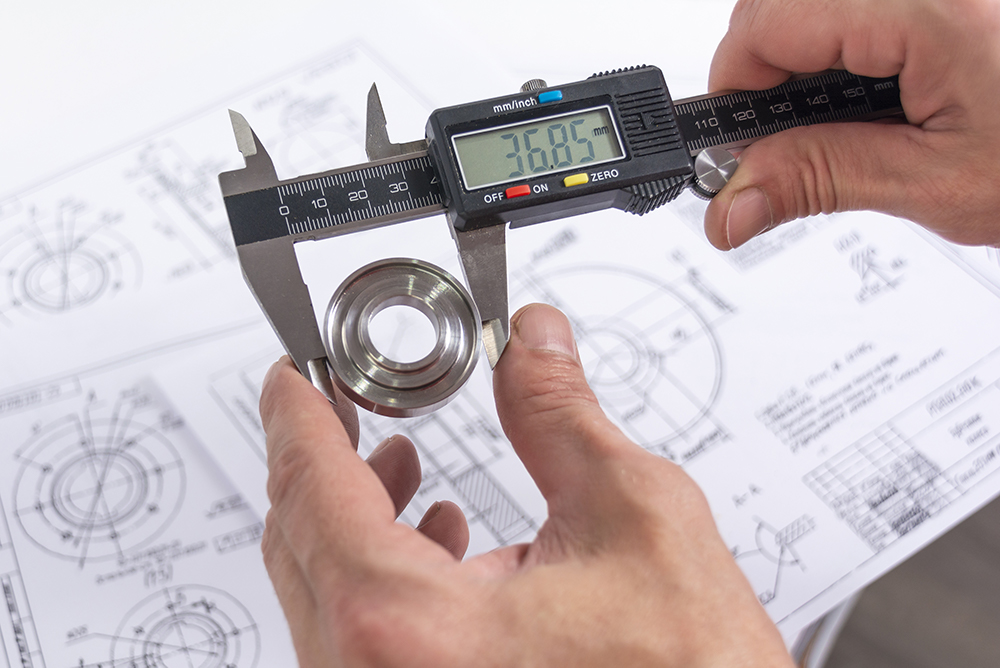
One of the remarkable features of precision casting is the high dimensional accuracy.
Compared to other casting processes, the deviations in the precision casting process are minimal.
Tolerances of a few tenths of a millimeter are often achieved, allowing enormous precision especially for highly complex components.
They show fewer deviations and exactly meet the specific requirements and tolerances required for their application.
Another major advantage of precision casting is the ability to create very complex and difficult shapes and structures that would not be possible with other casting techniques.
Precision casting technology is compatible with a variety of materials, from unalloyed steel to stainless steel alloys, aluminum and bronze.
Another characteristic is the excellent surface quality. Components made by precision casting generally have a very smooth and clean surface. This often reduces or eliminates the need for subsequent machining or surface finishing.
Thanks to our expertise in investment casting and surface treatment, we guarantee a high surface quality of our products. This makes them not only extremely functional, but also visually appealing.
Despite the high quality and precision, precision casting can be more cost-effective than other techniques in many cases. The ability to create a production-like final form can significantly reduce the need for expensive post-processing.
Compliance with the highest quality standards is a matter of course for us.
Our integrated quality management system guarantees that every product that leaves our warehouse meets our strict quality controls.
Our efficient production process and the strategic positioning of our production facilities allow us to offer high quality products at competitive prices.
The use of state-of-the-art technology and efficient production processes allows us to keep component and tooling costs low without compromising on quality.
We are proud to be able to offer our customers a “free house” service. This means fewer complications and time savings for you, as we handle all the logistics from production to delivery to you.
Our commitment to excellent customer service is a central pillar of our corporate philosophy.
Our team of experts is available to assist you from initial contact through product delivery, ensuring that your specific requirements are met efficiently and to your complete satisfaction.
Our innovative design and engineering team specializes in translating your ideas into precise technical drawings and designs (CAD).
We work closely with you to understand your requirements and develop the best possible solutions to meet your specific needs.
We verify that your components are designed for investment casting, redefine the required tolerances, and determine the material allowances for machining.
We revise your drawings and adapt the standards and specifications to the requirements for quality castings.
Your advantages.
Investment casting: an industry standard.
Investment casting is a highly developed technique characterized by its ability to produce precise and detailed components.
The special properties of investment casting, such as high dimensional accuracy, surface finish, the ability to produce complex geometry and compatibility with a wide range of materials, have made it the preferred process for producing high-precision components. This casting process is used in numerous industries: Sufficiently from the automotive industry to mechanical engineering to modern medical technology.
But why has investment casting gained such importance?
Investment casting helps to meet even difficult and precise requirements that other traditional processes often cannot achieve.
For example, while conventional casting often requires extensive post-processing, investment casting often enables a near-finish mold that reduces or in some cases makes redundant further processing steps.
In addition, investment casting enables the production of components with considerable material savings and thus cost efficiency.
All these advantages make investment casting an indispensable component in modern production technology.
Whether you need a few special parts (small series) or large production quantities (large series), we adapt to your requirements and ensure that we meet your expectations in terms of quality, cost, and delivery time.
Are you interested?
Contact us for an individual offer or a free consultation.
Our process.
The steps of the investment casting process:
from prototype to perfection.
The investment casting process at LLOYD Industrial Parts is a high-precision manufacturing process divided into the following steps:
1. Contacting us
First, you contact us to give us insight into your specific needs and requirements for your part. At this stage, our experts will consult with you regarding the feasibility of your component, the materials to be used, and any other relevant factors. We are also happy to assist with design and drawing.
2. Production of the tools
In the next phase, the molding tools are produced. These are used to create an accurate wax model of your component. They are usually made of aluminum and tailored to the customer's specific requirements.
3. Wax model construction
In the next step, the injection mold is used to create an accurate wax model of your component. The wax models represent the final product in its final form and serve as the master for the subsequent process step.
4. Ceramic build-up and lost wax process
Now the wax model is embedded in a ceramic shell. For this purpose, the wax model is doused several times with ceramic slip and sprinkled with fine ceramic sand. After sufficient drying and hardening of the shell, the wax model is melted out - a high-precision, hollow ceramic mold remains.
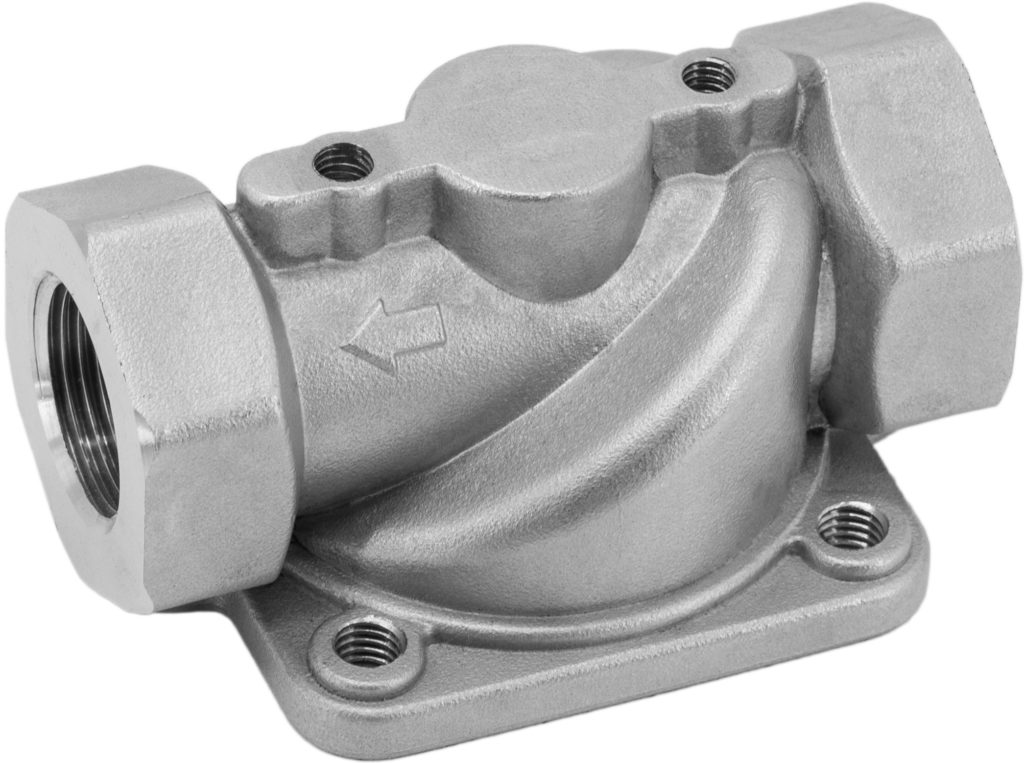
5. Casting of the melt
Now the actual investment casting takes place. The previously heated ceramic mold is poured out with the molten metal. After cooling, the ceramic shell is removed and the raw casting becomes visible.
6. Finishing, mechanical finishing and assembly
This step involves mechanical finishing of the casting to remove casting flash and skins. Depending on requirements, heat or surface treatment may be applied before the components move on to subassembly.
7. Final quality control
We perform strict quality control to ensure that all components produced meet requirements. We use the latest inspection techniques to ensure that the required quality standards are met.
8. Packing and shipping "free of charge"
After successful quality control, the components are securely packaged and shipped to you "free house". In each of these steps, we apply our expertise and experience to ensure that you receive the best quality and performance for your components.
FAQ
Frequently Asked Questions
Why is it called investment casting?
The term investment casting is derived from the fact that this process can be used to produce very fine, detailed and precise components. It enables the production of workpieces with complicated shapes and high demands on dimensional accuracy.
Is there a minimum order quantity?
The minimum order quantity for investment casting is highly dependent on individual requirements and circumstances. In principle, however, investment casting is also suitable for the production of smaller quantities. However, you should consult your contact person individually.
Are the final components ready for installation?
As a rule, investment castings still require finishing after the actual casting process. This includes deburring, machining of defined areas, heat treatment if necessary, and surface treatment or painting.
What alloys are used?
A wide range of materials can be processed using the investment casting process. Various steels and stainless steels, aluminum alloys, brass alloys, copper alloys and various special alloys are frequently used.
What is investment casting used for?
Investment casting is mainly used in the production of components and parts with high contour accuracy and complex shapes, where conventional casting methods reach their limits. Areas of application include mechanical engineering, the automotive industry, the aerospace industry, medical technology and jewelry manufacturing.
How are castings produced in the investment casting process?
In the investment casting process, a model of the desired component is first created from wax or plastic. This model serves as the starting point for creating a casting mold from heat-resistant material, usually ceramic. The model is then melted out (lost wax process) and the resulting hollow mold is poured with the liquid material. After cooling and hardening, the mold is broken open and the casting is removed.
What casting processes are there?
There are a variety of casting processes. In addition to investment casting, the sand casting process, the die casting process, the permanent mold casting process and the centrifugal casting process are also common. Each process has its specific advantages and is used depending on the requirements of the workpiece.
What types of casting molds are there?
There are different types of molds that are used depending on the casting process chosen. These include, for example, models made of wood or metal for the sand casting process, metal molds for the die casting process, or wax models for the investment casting process (lost wax casting).
How does the lost wax process work?
In the lost wax process, a wax pattern of the part to be produced is embedded in a refractory ceramic material. After the mold hardens, the wax is heated and thus melted out, creating a perfect, hollow replica of the part. The metal is poured into this mold, and after solidifying in the mold, it takes on the shape of the original model.
What is the difference between investment casting and gray casting?
Gray cast iron is cast iron with lamellar graphite inclusions. It is easy to cast and is characterized by its high damping of vibrations. Investment casting, on the other hand, is a process and not a material. A wide range of materials, including gray cast iron, can be used in investment casting. The difference therefore lies in the different areas of application and the specific properties of the materials or processes.
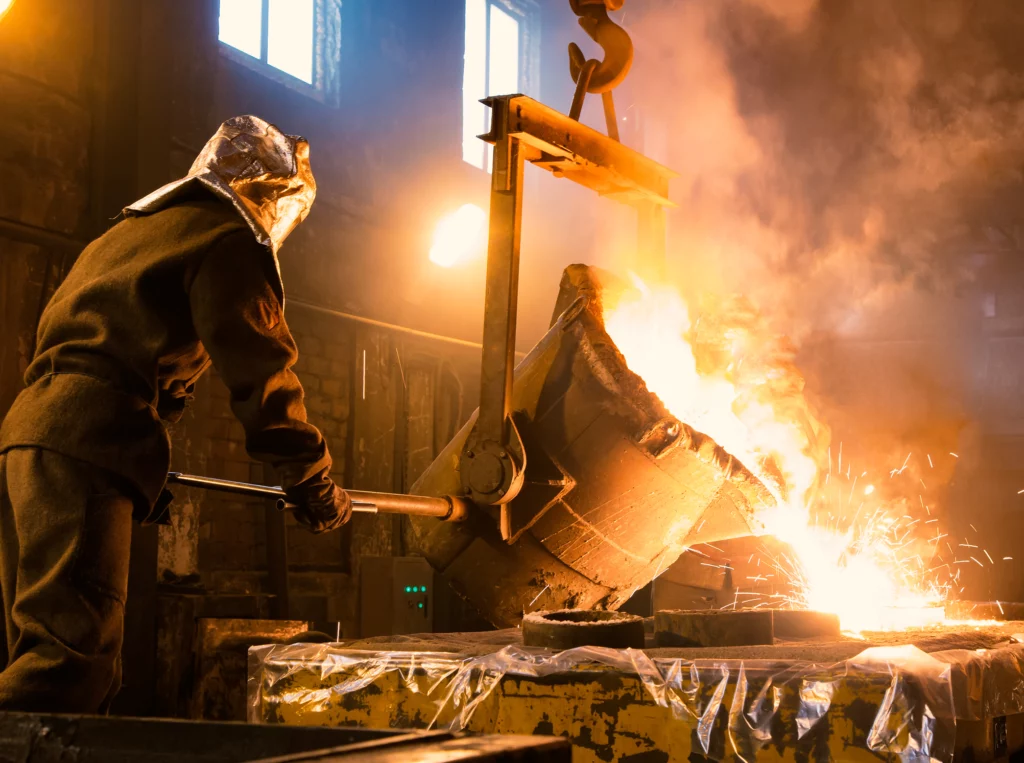
CONTACT US.
Our professionals are ready to answer your questions about the production of precision casting parts, discuss technical details, or create a quote for your next project.
We cordially invite you to take the first step and contact us – by phone, email, or via our online contact form on our website.
Following the North German motto: Just give us a call.
E-Mail: info@lloyd-parts.de
Phone: +49 421 835 265 20
Service offer
Further services
In addition to our core competence in investment casting, we offer a wide range of additional services that can optimize and simplify your production processes. Expand your range of services with our all-round carefree packages.
Metal Injection Molding (MIM)
With the MIM (Metal Injection Molding) process, we offer you an advanced technology for manufacturing precise and complex metal parts of the highest quality. This method allows for the processing of a wide range of metallic materials with almost unlimited design possibilities.
CNC manufacturing
Various milling and turning techniques allow us to realize complex shapes and contours according to your specifications.
Component assembly
Our range of services also includes the assembly of components. We take on the assembly and adjustment of individual parts into functional units, allowing you to focus on your core competencies. With state-of-the-art technologies and precisely according to your requirements, we assemble efficiently and with high quality.